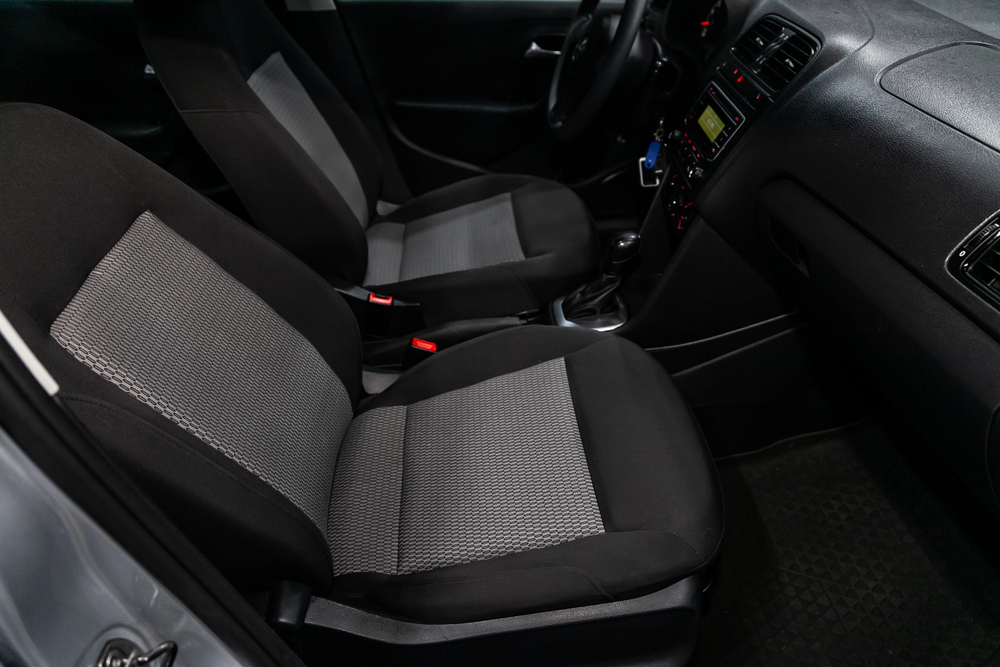
As an ongoing initiative, this collaboration emphasizes customization, precision manufacturing, and robust quality control measures to support the client’s production processes and align with their delivery timelines.
Project Specifications
Quality Control Steps
Incoming Material Inspection
In-Process Inspections
Final Inspection
Project Highlights
Next Steps
Manufacturing Details
1. Material Preparation
Base Material: 100% woven polyester engineered for varying firmness levels to suit different seating applications.
Customization: Red Hytrel strip integrated at 5-inch intervals for automotive fabric to aid in precise seat assembly alignment.
2. Fabric Production
Weaving Process: High-precision weaving ensures uniform tension, strength, and structural integrity across all fabric rolls.
Dimensional Consistency: Fabrics are produced in specified widths and lengths to minimize material waste and streamline the client’s production process.
3. Roll Slitting and Re-Rolling
Rolls are slit to required widths and re-rolled, with inspections for length accuracy, edge quality, and consistent tension.
Each roll is labeled with essential product details, including serial numbers and manufacturing dates, for seamless inventory management.
4. Packaging and Delivery
Rolls are wrapped and moisture-protected to ensure safe transport.
Documentation, including Certificates of Analysis, flammability test reports, inspection maps, and packing lists, is prepared and sent ahead of shipments.
This ongoing project demonstrates Acme Mills’ ability to provide customized, high-performance suspension fabrics that align with client needs across multiple industries. Through close collaboration, precise manufacturing, and rigorous quality assurance, Acme Mills is supporting the client’s production of innovative seating solutions and reinforcing its position as a trusted supplier in competitive manufacturing markets.