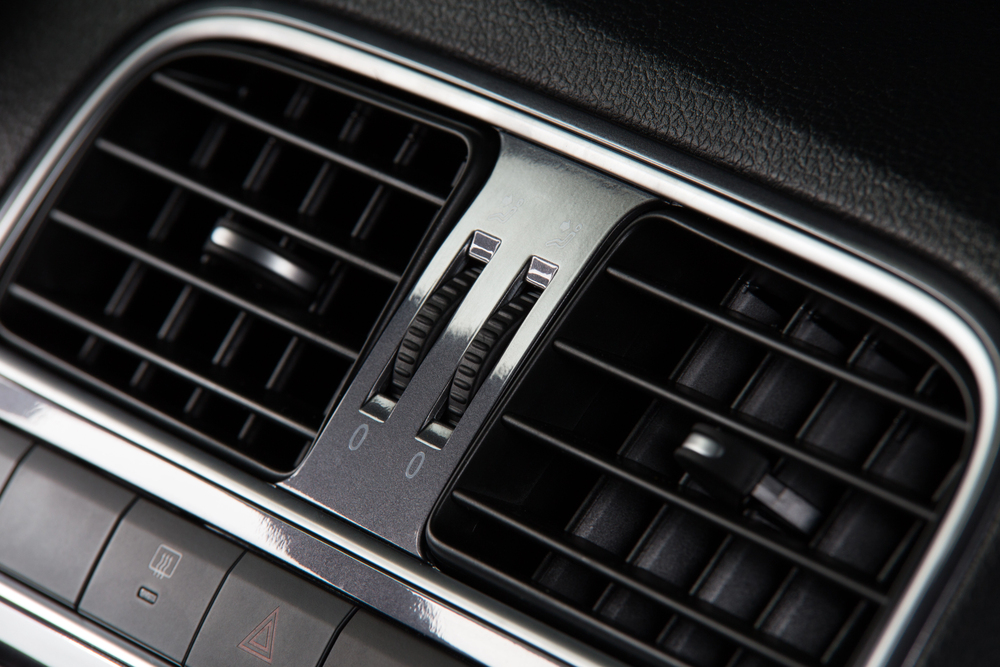
Project Specifications
Manufacturing Details
1. Material Preparation
Base Material: High-strength spunbond polyester filaments, selected for durability and stability.
Fiber Composition: Engineered to achieve optimal tensile strength and minimal elongation for consistent performance during molding.
2. Fabric Production
Spunbond Process: Continuous polyester filaments were extruded, stretched, and bonded to form a uniform scrim with a precise weight and thickness.
Customization: Scrim rolls were produced in specific widths and lengths to match the client’s mold dimensions, minimizing material waste.
3. Roll Slitting and Re-Rolling
Scrim was slit to required widths and re-rolled for efficient handling and transport.
Each roll underwent inspection during re-rolling to confirm accurate length, tension, and edge quality.
4. Packaging and Delivery
Rolls were moisture-protected and securely wrapped for transportation.
Shipments were labeled according to client specifications, with detailed bill of lading documentation to facilitate seamless inventory management.
Quality Control Steps
Incoming Material Inspection
In-Process Inspections
Final Inspection
Project Highlights
This project demonstrates Acme Mills’ expertise in delivering high-performance materials for compression molding applications in the automotive industry. By providing customized spunbond scrim with precise material properties and adhering to rigorous quality control processes, Acme Mills supported the client’s production of durable, high-quality air vent systems for major automotive OEMs. This collaboration highlights Acme Mills’ role as a trusted supplier of innovative material solutions for demanding manufacturing environments.